Environmental proofing is the secret to long life – Kempower chargers have low life cycle costs thanks to the Finnish treatment
We build chargers that last. For you this means low life cycle costs and more predictable maintenance. How do we do this? By putting our chargers and their components through the Finnish treatment, and by offering software tools for preventive maintenance to ensure a long and trouble-free life.
Durable chargers save time and money for our customers, which is exactly why we have made them our priority. EV chargers often face tough conditions, but with the product design experience of our sister company Kemppi, we have figured out some clever solutions to battle them.
Durable chargers have more protection than the standards require
There are three things to consider when building chargers that last: adhering to the international standards for electric appliances and EV chargers, such as IEC-61851, designing a dust- and leak-proof case, and protecting the electronics inside the case.
The international norms dictate the protection class of the case, but we don’t settle for that baseline. Our environmental proofing doesn’t rely solely on the casing. Instead, we focus on two things: protecting the electronics and designing the layout of the charger so that it repels dust and condensation.
Petri Korhonen, Kempower Chief Engineer
Here at Kempower we have designed a specially made thick lacquer, which is applied by a robot, for protecting the electronics inside the charger. The composition of our lacquer makes it possible to have a thicker and more durable layer than would be possible with other methods.
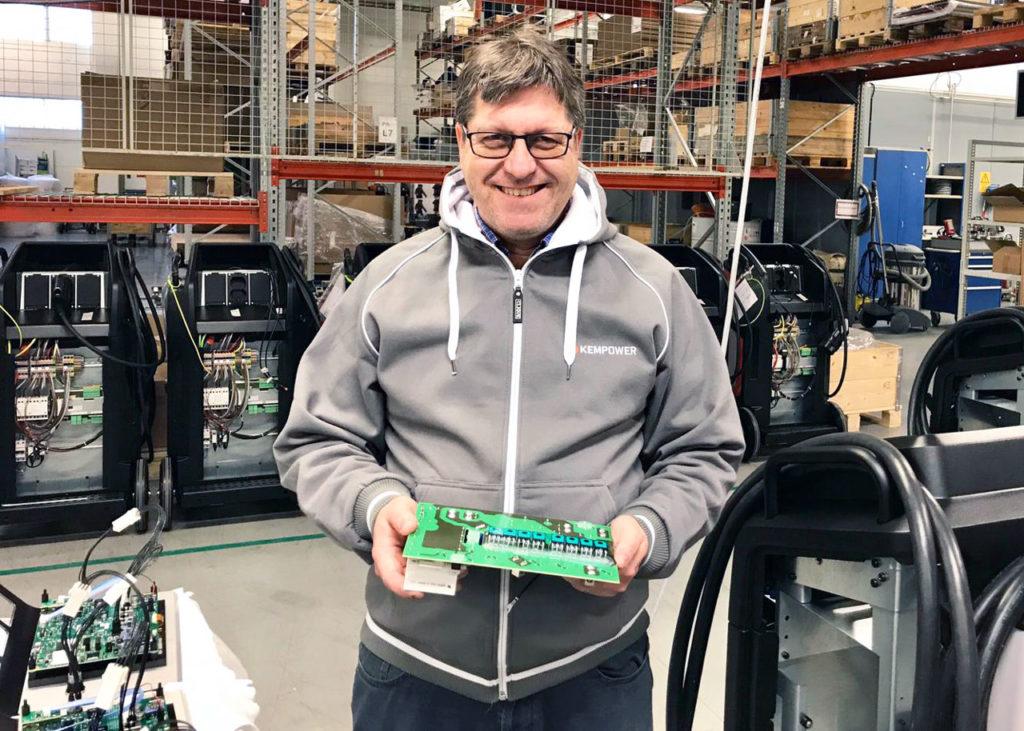
Environmental proofing protects against condensation and corrosion
Clever solutions for environmental proofing are crucial, since almost all EV chargers are installed outdoors. Ideally, they would have shelters like the ones built for gas pumps, but instead are often left out in the open to endure changing weather conditions. And if the charger is located, say, in a seaside city where the air is salty or in a city where there are more pollutants in the air, there will be corrosion to deal with in addition to humidity.
Petri Korhonen
Finland has some steep changes in temperature and air humidity throughout the year, but according to Korhonen, those are easy to account for. It is when corrosive compounds are added that you risk malfunction or premature failure of components. Corrosive compounds can drastically shorten the lives of unprotected materials and components. Dust can also create similar problems when it gets into a machine’s insides.
The dust you have in machine shops can be conductive. If it gets into your insufficiently protected appliance, it will cause big issues. Saltwater is conductive, and often the dust in mines is too.
Petri Korhonen
Testing components and chargers weeds out weaknesses
Important steps in ensuring longevity for our chargers are taken with testing the components used in the assemblies. We run short-term and long-term tests on all critical components before accepting them for use. We test for issues such as excess current and voltage.
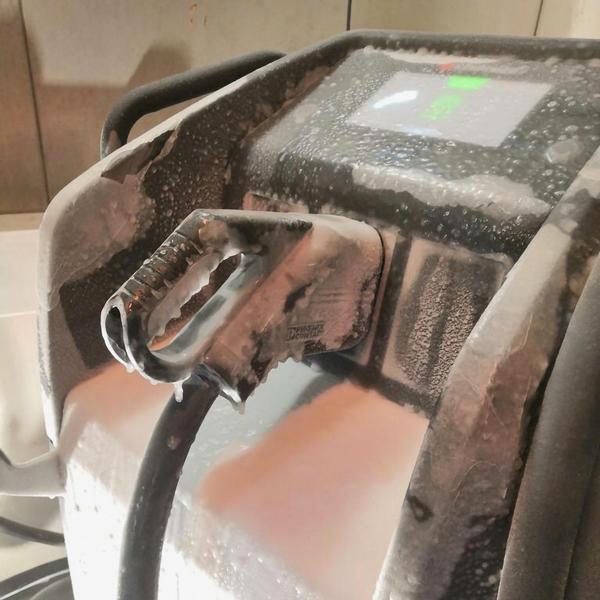
We test all core components that could be a risk for reliability. These include power semiconductors, for instance. For evaluation, we have created our own Kempower design rules. They are based on the component manufacturer data sheets, but we have created our own baselines for what we know the component should be able to endure according to our tests.
Petri Korhonen
In addition to testing the components, we also do heavy type-testing on the whole charger. We do endurance tests with 12,000 charging cycles, where every dial on the charger is turned to full power.
The most stressful situation for the charger is letting it cool down for a short period between these full power cycles. The tests are designed to be far worse than anything the charger will have to endure during normal use.
Petri Korhonen
The most expensive type of maintenance is unexpected maintenance
Our chargers are fitted with sensors that monitor parameters such as temperature. This way we can monitor the charger and, if a rise in any measured parameter value is detected, we are able to alert the maintenance crew. So maintenance can be planned ahead and unexpected shutdowns can be avoided.
Petri Korhonen
Kempower chargers have a modular structure to make maintenance as easy and cost-effective as possible. If a module needs to be changed, a replacement can be ordered from Kempower and sent to your company’s own mechanics – no need to send the whole charger to us. The modules can be individually replaced with no special knowledge needed from the maintenance personnel.
Experience with Kemppi gives Kempower an edge in the growing EV charger market
Sister company Kemppi’s knowledge in designing and manufacturing welding machinery for tough conditions such as shipyards, offshore and metal workshops has proven an important advantage for Kempower. Welding machines are also often used in challenging conditions like outdoors in changing weather and even underwater, so Kemppi has tried and tested solutions that work reliably in harsh environments.
Others may struggle with solutions that are in our DNA, and sometimes we don’t even realise the uniqueness of certain solutions – they are so obvious to us.
Environmental proofing and durability are becoming more and more important in chargers, as attention turns increasingly to life cycle costs with growing companies and fleet sizes.
Companies with larger fleets and growing experience in managing them are paying more and more attention to what it all costs: how much maintenance is, and what percentage the initial investment of the purchase amounts to. This type of fleet management thinking draws closer attention to life cycle costs and the ways of lowering them. And this is where Kempower shines.
Petri Korhonen